INSIGHT > HAIX
Give sub-par footwear the boot
Headquartered in Bavaria, with a sales office in Kentucky and factories in Germany and Croatia, Haix has built up a worldwide reputation as a ‘safe brand’. UK Sales Manager Simon Ash explores how protective footwear has evolved and the key factors to consider when purchasing PPE…
The history of safety boots can be traced back to the 20th century. Before this time, it was cheaper and faster to replace injured workers than to introduce safety measures or provide personal protective equipment (PPE).
It was the introduction of liability insurance costs that first made larger corporations take notice and start focusing on protecting their workforces. Invented at the end of World War Two, steel toe boots originated in Germany, and were designed for the military; built to stand the test of time and offering durable and robust foot protection.
In 1970, the United States enacted the Occupational Safety and Health Act that aimed to improve working conditions and create safer environments for workers. The standard included the use of protective footwear for workers that worked in situations which could pose a risk of foot injuries occurring.
Today in the UK, under the Health and Safety at Work Act 1974, wearing protective shoes or boots is a legal requirement in several industries such as construction or manufacturing. Employers have a duty to protect the ‘health, safety and welfare’ of all their employees at work, as well as others on their premises, ensuring the assessment and implementation of appropriate controls to manage potential risk and suitable provision of PPE.
Safety footwear is an essential part of PPE that provides protection against risks such as slips and trips, sharp, moving or falling objects, electric and chemical exposure, poor weather conditions and musculoskeletal disorders.
It is important to get footwear right. Though not wearing safety footwear can be detrimental, the risk of wearing poor quality boots can be just as critical. The current standard for safety footwear across Europe (EN ISO 20345:2011) requires all safety footwear to have toe protection against a 200 joule impact and a 15KN compression test; the equivalent to the amount of energy and weight it would take before breaking the toe region.
There is no one-boot-fits-all rule, unfortunately. Not all safety shoes or boots will be ideal for all working environments. For this reason, employers need to ensure the boots purchased are fit for purpose and will protect workers against the risks they face. There are several key factors to consider for footwear…
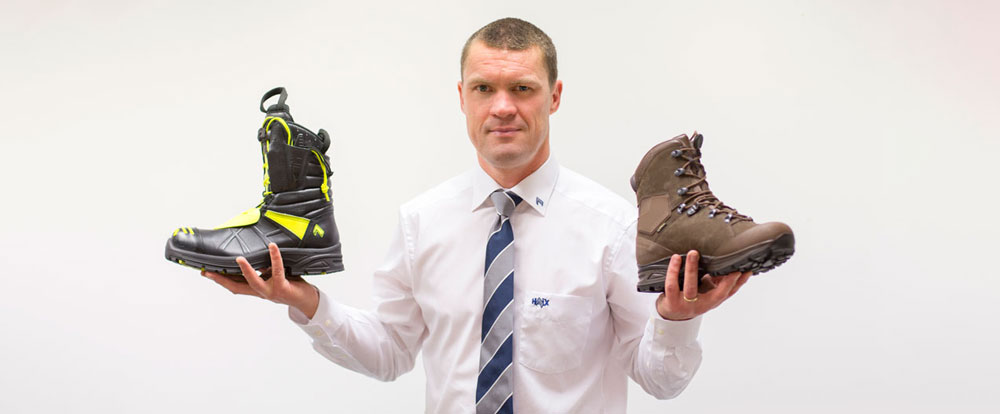
Simon Ash, UK sales manager, HAIX
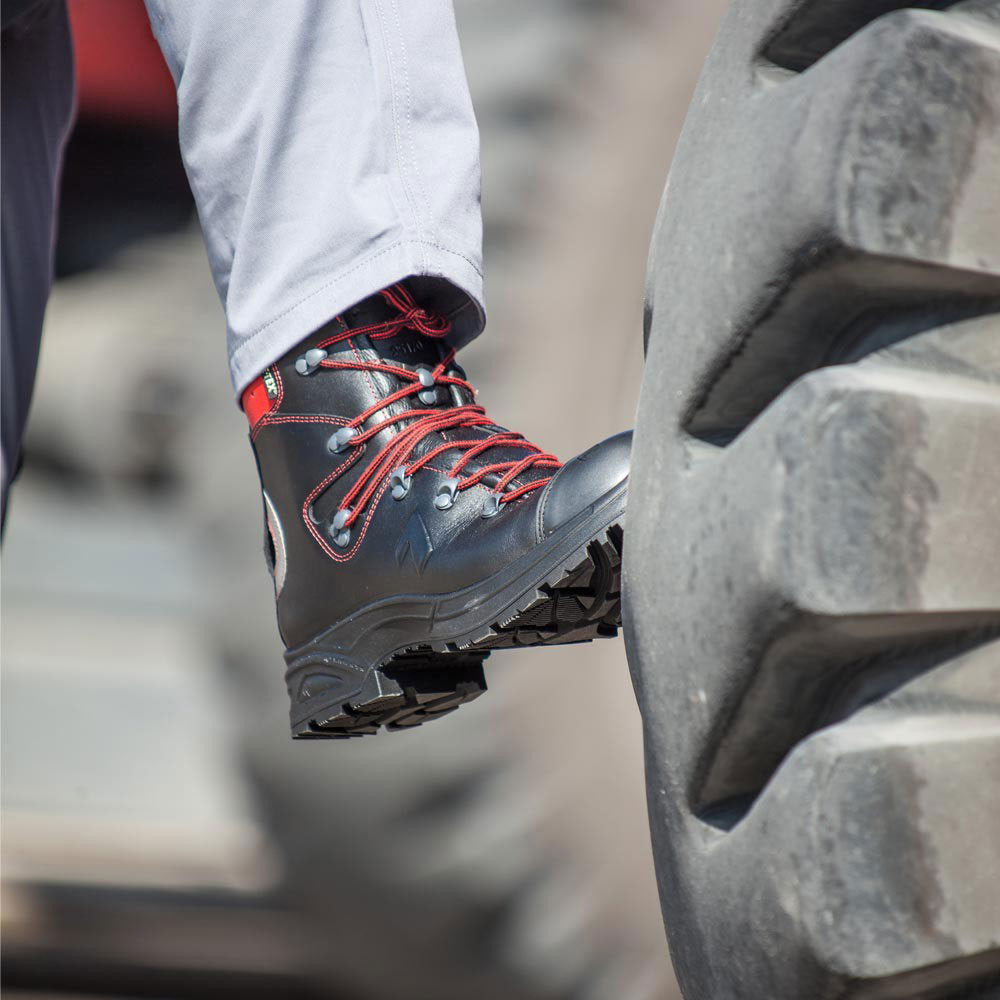
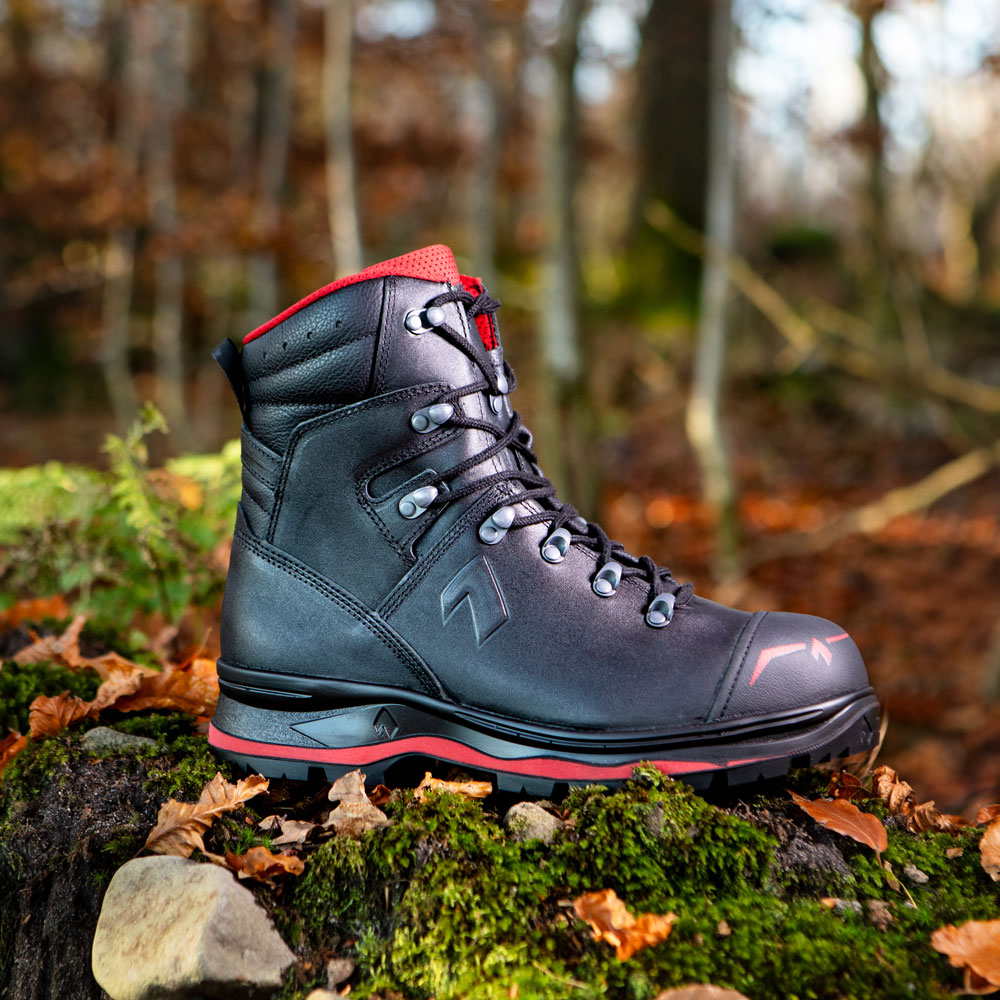
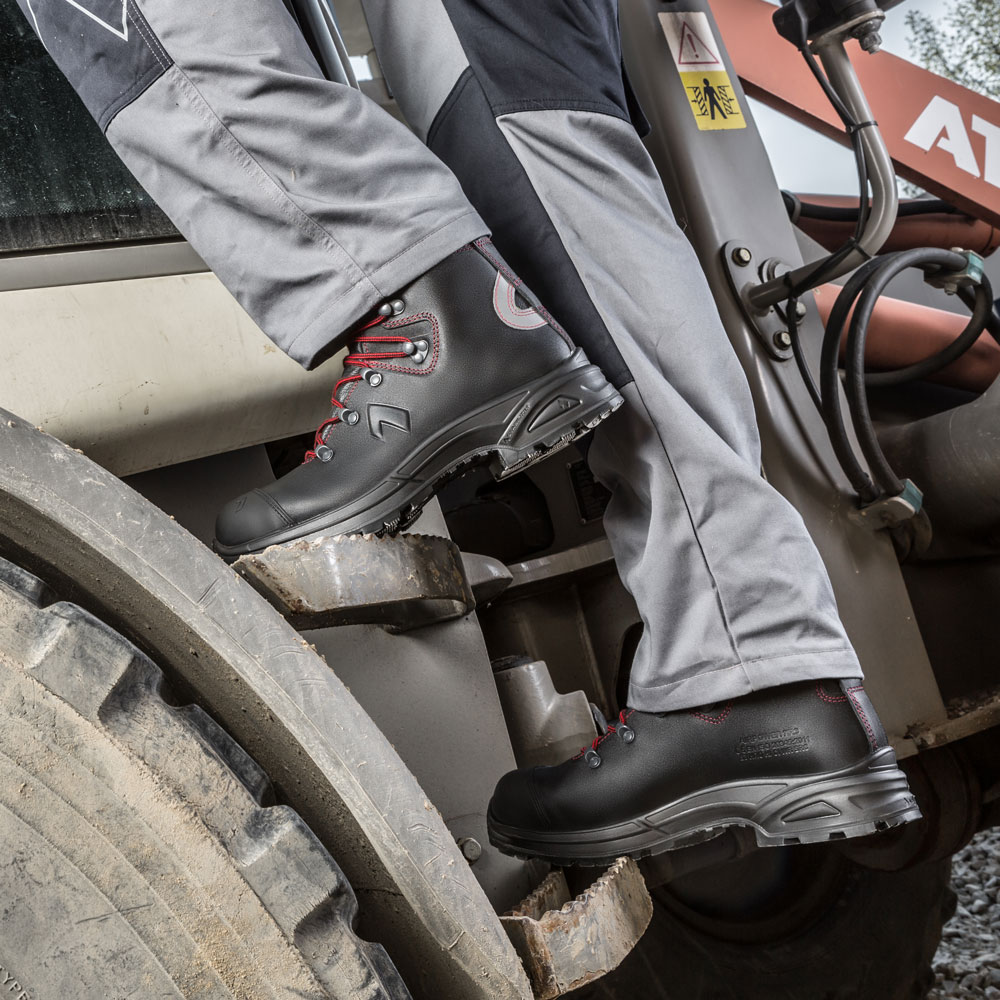
COMFORT
Models designed with an arch support help to stabilise feet and maintain an employee’s correct posture, reducing harmful effects of impact-related stresses when the foot strikes the ground. It is also advised to look for an easy lacing system so that the process of putting boots on and taking them off at the end of the day is quick and easy.
FOOT SHAPE
The shape of the foot fluctuates throughout the day. Ideally, boots should be tried on in the afternoon, when feet are at their warmest, to determine an accurate size. This will ensure a comfortable fit throughout the working day.
QUALITY OVER CONVENIENCE
Accidents are expensive. There are many hidden and uninsured costs that, as the employer, you will be liable. There is a temptation to skimp and save money but improper use of PPE that leads to an injury or fatality could mean substantial fines for the company, even imprisonment.
Budget safety footwear costs the manufacturer less to make which means features such as comfort, breathability and ankle support may not be high priority. With footwear you tend to get what you pay for. Budget boots have a shorter lifespan and will need to be replaced more often, whereas making the investment in high quality boots could see you through for 10 years – still suitably equipped with a good level of protection.
PROTECTION
Choosing the right level of protection you need for the job could mean incorporating anti-slip, puncture-resistance, protective toecaps, waterproofing and breathability. When selecting safety footwear, it is important to carry out a proper risk assessment and consult an expert for advice and guidance.
TRY BEFORE YOU BUY
PPE is personal for workers, and some may have a pre-conceived idea of what’s ‘good’ or ‘necessary’ PPE, while others may not understand its importance at all. If workers do not understand why they need to wear PPE, or don’t have any say in choosing it, they are more likely to reject it, some may even refuse to use it. We expect workers to wear their safety kit every day, it’s natural there would be some push back if their PPE is uncomfortable, not the right fit or bulky and unattractive. Wearer acceptance is one of the biggest hurdles to overcome when it comes to PPE.
In order to avoid an unhappy (and at-risk) workforce, try involving them in the PPE buying process; taking into account their preferences. Ask your workers about their current PPE, what it is they like and don’t like about it, and show them the options you are thinking of purchasing. Having this conversation and giving them a choice may make them more likely to accept it and will also give them a sense of empowerment in that they’ve contributed to the selection process.
Sometimes, unfortunately, this won’t be enough, and a harder sell may be needed. In this case, demonstrate the consequences of not wearing their PPE: what could happen, what would this mean for them, their job, their health, and hone in on why PPE is in place and is in their best interest.
Communicating the real, positive impact that PPE has and encouraging an open conversation should drive a positive change and create a more productive, safer culture.