FOCUS > SPECIAL FASTENERS
Special fasteners for specific requirements
Owlett-Jaton, Hague Fasteners, Nufast, Dejond and SFC (Europe) feature in our round-up...
Owlett-Jaton
Adding value by going the extra mile
Owlett-Jaton offers a wide range of secondary processes to enhance its comprehensive stock range and provide customers a variety of solutions. Its range of subcon services features more than 16 surface finishes, as well as five different thread locking/sealing patches on the standard, stocked fastener range.
Finishing services include electroplating, organic finishes, locking, sealing patches and machined modifications. Owlett-Jaton also sources and manufactures bespoke non-standard fastening products to customer specifications; these too can benefit from secondary processes where required.
Electroplated and organic finishes are applied to prevent corrosion and for aesthetic reasons. Additional topcoats can also be applied to assist with torque tensioning control. The most popular finishes provided are Organic, Zinc Flake and Bright Zinc plated parts, with a variety of coloured passivate.
Thread patching is also available, ensuring parts are securely locked into position after assembly, so resisting loss of clamp load due to vibration. By applying a nylon patch to the thread of (mainly) bolts, set screws and socket sets, performance can be improved. Additionally, thread patches can seal assemblies in gas, oil and other liquid industries, helping prevent leakages.
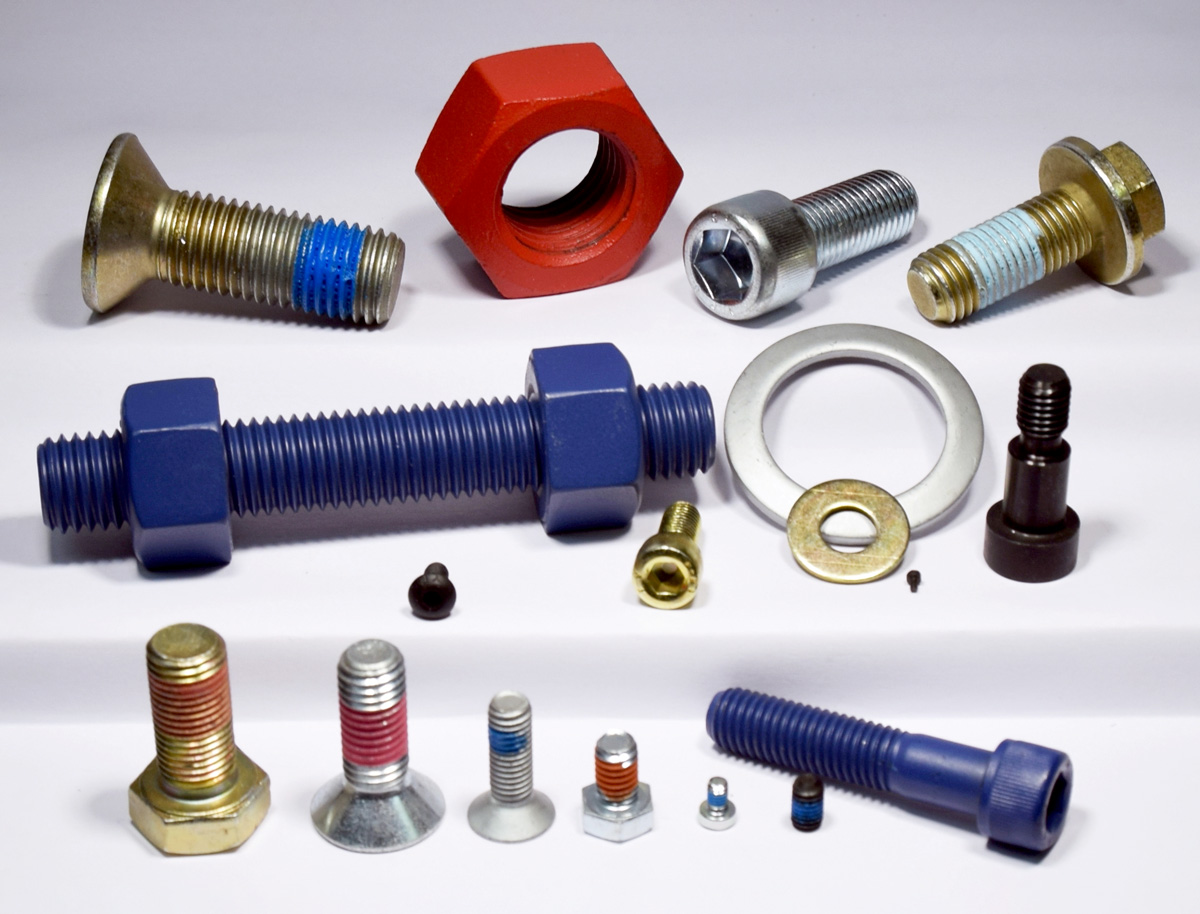
Other services include simple drilling to allow the insertion of locking split pins, to more complicated modifications such as cutting and re-threading and shank diameter reduction.
By partnering with reliable subcontractors for these processes, Owlett-Jaton offers a reliable, fast and efficient turnaround, providing enhanced products via a one-stop service.
A dedicated finishing team handles orders for all specially finished parts, tracking customer orders from placement, through the plating process, to final delivery.
With customer service and quality assurance at the forefront, all parts are inspected by the QC team before despatch. Batch traceability is maintained throughout, ensuring the manufacturing processes can be fully audited back to the part manufacturer. Initial Sample Inspection Reports (ISIR) and Production Part Approval Process (PPAP) certification up to level 3 on products are available, and quality is approved to BS EN ISO 9001:2015.
Hague Fasteners
49 years of critical bolting quality and material traceability
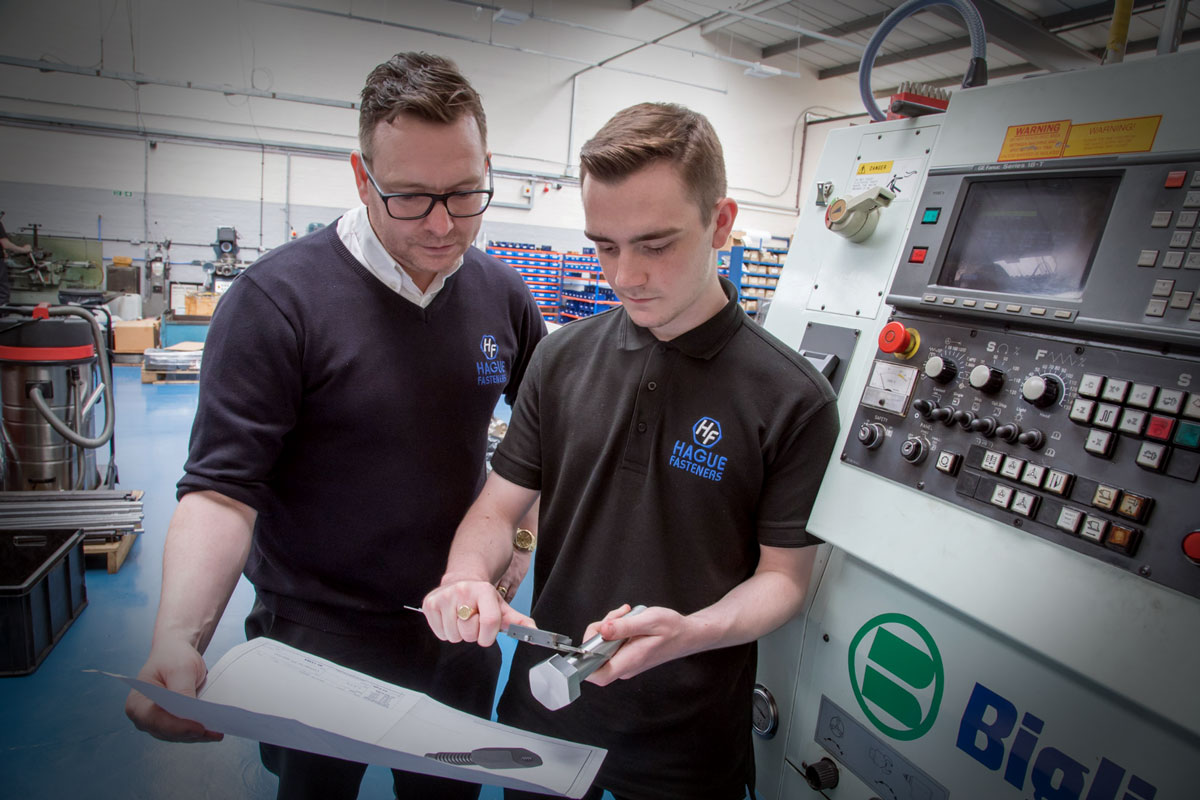
Hague Fasteners is one of the longest-established, family-run, UK manufacturers of Heat Exchanger Special Fasteners and Precision Engineered Components for all critical applications and environments for all industries including oil & gas, offshore, construction, subsea, power generation and high-pressure locations.
Established in 1971, Hague has perfected critical bolting quality and material traceability and is renowned for high integrity, fully traceable bolting, with highest level QC1 Fasteners manufactured and fitted to some of the world’s most critical structures and facilities, giving total quality assurance.
Hague has tight controls and policies on European origin material, backed by sourcing and manufacturing accreditation to Pressure Equipment Directive 2014/68/EU by BSI, with expertise in the smaller batches of custom parts where environments dictate the need for total reliability. No quantity is too small for Hague to sort your supply needs.
Hague Fasteners carries a wide range of fully tested and traceable materials from common carbon steels through to the highest performance superalloys, enabling the rapid production of any items to international standards or to unique designs and drawings.
Operating from its customised manufacturing facility in the West Midlands, Hague exports all over the world. Chemical, metallurgical, mechanical and non-destructive testing is all performed at accredited laboratories to give independent verification of processing and manufacturing controls.